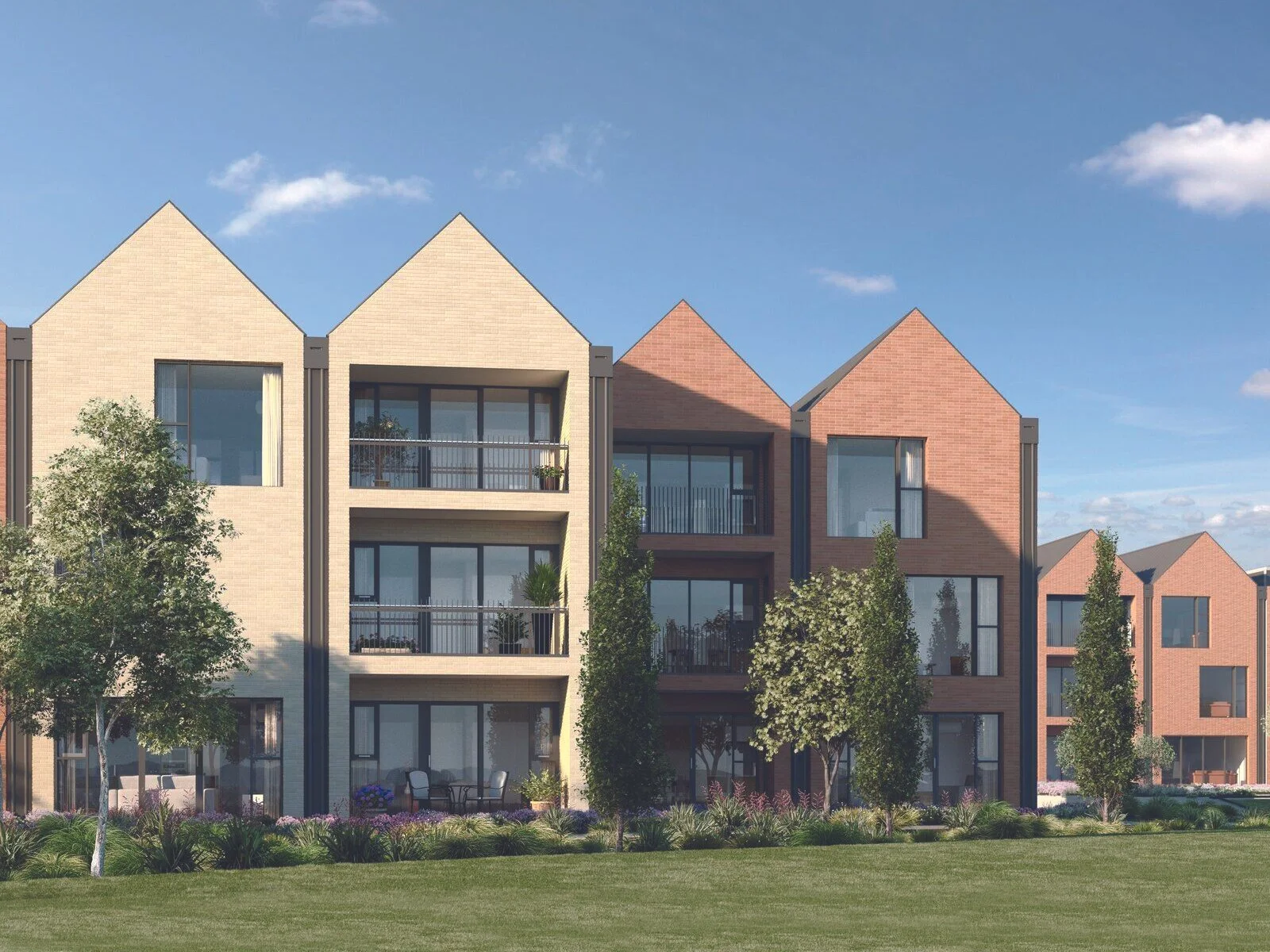
Ryman Healthcare Retirement Village Case Study
The building is the third of five apartment blocks in the Kevin Hickman Retirement Village in Christchurch. The apartment building has three above-ground levels with basement parking. There are a total of 27 apartments with a mix of two and three bed options.
The CLT structure starts at the ground floor walls and includes two suspended CLT floors with LVL supporting structure. The basement structure is concrete. The Gross Floor Area (GFA) is 4,444m².
KEY LEARNINGS & INSIGHTS
-
Time Savings
Mass timber construction saved 50% of the time required for the superstructure compared to traditional concrete methods. Contractors also reported faster installation for services like drilling and fixing into timber.Cost Considerations
Mass timber introduced a cost premium due to additional fixings, corbels, and fire-rated linings. However, early contractor and supplier involvement (ECI/ESI) was identified as a key method for mitigating these costs in future projects.Reduced Transport and Site Work
Truck movements were reduced by 65%, and on-site hours for the timber structure decreased by 45-55%. -
Carbon Reduction
The mass timber structure achieved a significant carbon saving, with 666,589 kg CO₂e compared to 2,039,150 kg CO₂e for concrete and steel.Lower Material Weight
Timber reduced the structural weight by over 50% compared to concrete, enabling lighter foundations and reducing environmental impact. -
Acoustic Performance
SoundDown™ acoustic systems ensured compliance with NZBC standards (STC 55, FSTC 50) for intertenancy walls and floors, demonstrating timber’s capability to meet sound insulation requirements.Seismic Design
Tectonus seismic connectors and vertical seismic joints allowed the building to withstand and recover from earthquakes. -
Fire Safety
Initial designs required full encapsulation with fire-rated plasterboard, but the revised approach minimised encapsulation to essential areas (e.g., corbels and beams) while meeting compliance.Moisture Control
Consistent moisture management and early planning were critical, especially for areas exposed during construction. -
Design Coordination
Early involvement of contractors and suppliers was crucial for optimising design, addressing challenges, and expediting decisions.Service Integration
Service route coordination for timber structures proved more complex than anticipated, emphasising the need for upfront planning. -
Prefabrication
CLT and LVL prefabrication improved on-site efficiency, with pre-assembled panels allowing immediate usability and reducing waste.Material Innovation
Use of advanced acoustic and fire-resistant systems highlighted timber’s adaptability to meet stringent residential requirements. -
Scaling Challenges
Limited suppliers in New Zealand highlighted the need for more competition and flexibility in sourcing materials. Supply chain challenges emphasized the importance of early supplier engagement.Knowledge Sharing
The project underscores the value of educating industry professionals on timber’s benefits and addressing misconceptions about its performance. -
Improved Work Environment
Workers found timber structures cleaner, quieter, and more pleasant to work with compared to concrete.Enhanced Living Spaces
The lighter, more sustainable materials contributed to a warmer, more aesthetically pleasing residential environment.