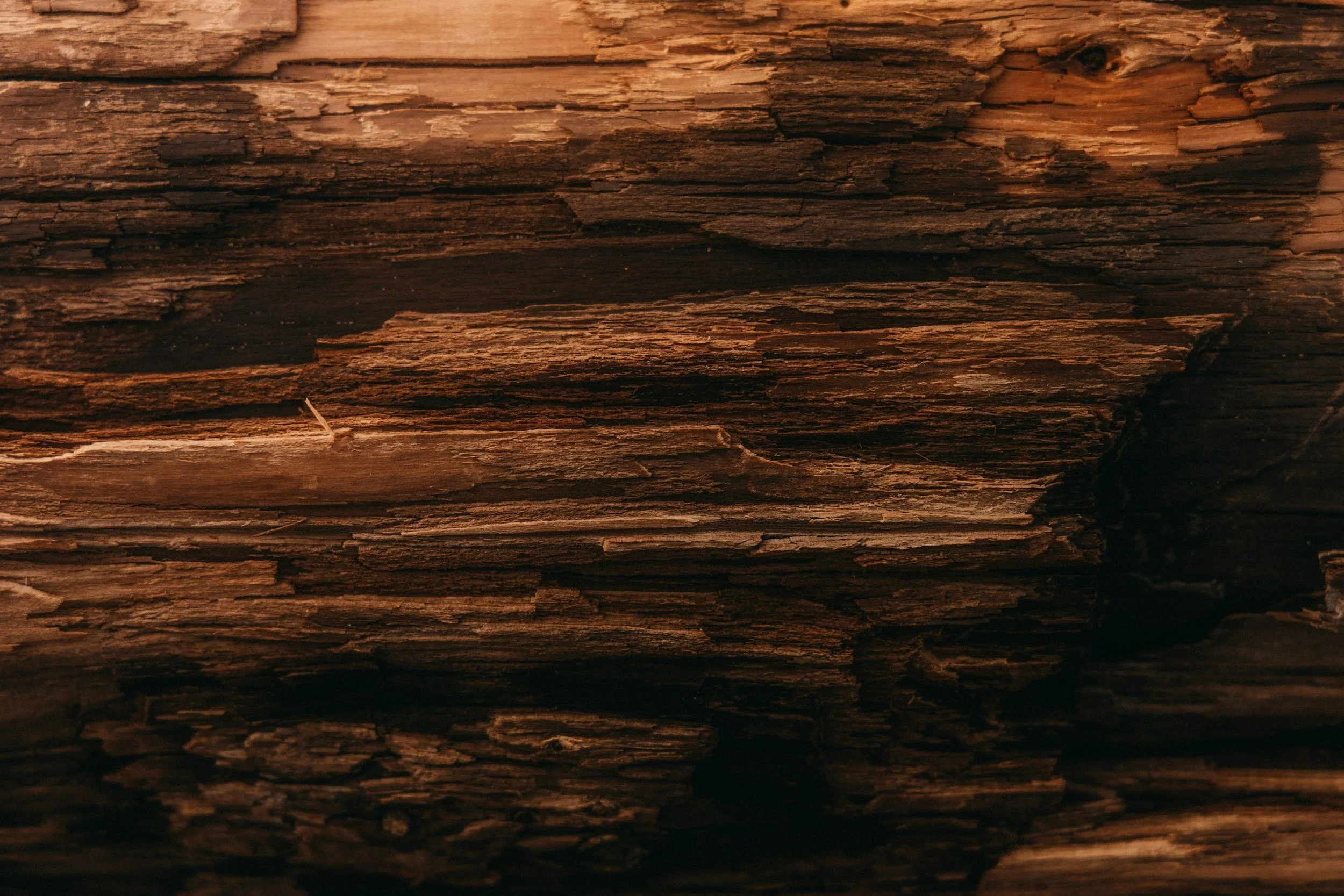
important lessons & insights from mass timber Constructions
These lessons extracted from case studies are to assist designers, specifiers and contractors in achieving efficient and cost-competitive mass timber buildings faster, particularly at concept and feasibility stages of design.
CLEARWATER QUAYS APARTMENTS, CHCH
-
Cost Comparison
While mass timber materials initially had a higher cost than concrete or steel, total out-turn project costs were 6% lower due to shorter construction timelines and lower development costs.Time Savings
Mass-timber construction saved 2.5 months during the critical frame-installation phase compared to traditional methods, leading to significant financial and logistical benefits. -
Carbon Footprint
The project achieved a net-negative carbon output of 87,500 kg compared to 800,000–950,000 kg of carbon emissions from concrete and steel builds.Reduced Waste
Off-site prefabrication minimised material waste and optimised efficiency, with recycled and sorted waste management practices further reducing the environmental impact.Traffic Reduction
CLT floors required fewer truck deliveries, significantly decreasing site traffic. -
Fire Safety
Solutions included intumescent coatings, sacrificial plywood layers, and fire-rated designs for intertenancy floors and columns, ensuring compliance with fire regulations.Moisture Control
A sealed façade system with a drained cavity and durable aluminium cladding ensured a weather-tight envelope, protecting the timber from external moisture. -
Team Integration
Engaging contractors, engineers, and designers early in the process led to more integrated solutions and streamlined workflows.Design Detailing
Mass-timber projects require more detailed and precise construction drawings upfront to reduce delays during the shop drawing phase. -
Digital Twin Models
3D BIM and cost modelling enabled accurate cost, carbon, and material analyses, facilitating data-driven decisions and optimal project planning. -
Demonstrating feasibility
This project serves as a reference for the cost, environmental, and practical benefits of mass-timber construction, encouraging broader industry adoption.Standardisation and supply chain
Increased market competition and improved prefabrication methods are making mass timber more accessible and competitive.
Waikato Regional Theatre
-
Programme Acceleration
Using CLT reduced on-site labour significantly. For example, blade walls required 27% less labour time compared to traditional methods, and CLT’s lighter weight allowed faster installation.Cost Savings
CLT reduced construction costs in multiple areas, such as:Blade Walls: Achieved a 13% cost saving over alternative materials.
Bleachers: Produced over 35% cost savings compared to precast concrete.
Auditorium Roof
Simplified design reduced temporary works and acoustic treatment costs, with an estimated saving exceeding 13%.
Improved Sequencing
Prefabrication and reduced cranage requirements streamlined workflows, moving certain elements off the critical path. -
Carbon Reduction
Substituting CLT achieved significant upfront carbon reductions across key elements:Blade walls: -78,357 kg CO₂e.
Bleachers: -43,040 kg CO₂e.
Roof: -72,770 kg CO₂e.
Sustainability Features
CLT’s low weight and prefabrication process reduced transport emissions and on-site waste. -
Acoustic Benefits
CLT’s density provided natural sound insulation and vibration damping, enhancing the auditorium’s acoustic performance without requiring extensive secondary treatments.Structural Advantages
CLT’s ability to function as both a substrate and diaphragm reduced the need for additional bracing, simplifying the design and installation process. -
Fire Safety
CLT’s inherent fire resistance minimised the need for additional materials in certain areas, although intumescent coatings were used on the exposed roof.Moisture Management
An extensive Moisture Management Plan (MMP) was implemented, including frequent testing and temporary protective measures during storage and installation. -
Integrated Approach
The project benefitted from a “one team” philosophy, with all partners contributing to CLT’s successful implementation through early design sketches and collaborative problem-solving.Shop Drawings
Coordination of shop drawings proved essential but time-intensive, highlighting the need for streamlined processes in future projects. -
BIM Coordination
A fully integrated BIM model allowed precise design updates, clash detection, and efficient coordination, ensuring accuracy in prefabrication and installation.Prefabrication
CLT elements were delivered pre-fabricated, reducing on-site adjustments and enabling faster assembly. -
Prefabrication
CLT elements were delivered pre-fabricated, reducing on-site adjustments and enabling faster assembly. -
Cultural Significance
The integration of heritage structures with modern design and a focus on riverfront connectivity created a space that celebrates local history and culture.Enhanced User Experience
Acoustic improvements and innovative design make the theatre a world-class venue for diverse performances, benefiting both the community and tourism.
hardy street apartments
-
Cost Comparison
While CLT had higher upfront material costs, the overall cost was competitive due to faster construction times and lower Preliminary & General (P&G) expenses.Time Savings
CLT construction allowed faster erection due to lightweight panels and prefabrication, reducing time on site and improving project efficiency.Economic Scaling
Repetition of the superstructure design across seven similar units enabled economies of scale. -
Carbon Sequestration
The project sequestered 470 tons of CO₂, significantly reducing its carbon footprint compared to traditional concrete and steel alternatives.Waste Reduction
Prefabrication minimised material waste on-site, enhancing sustainability.Lightweight Materials
The lighter structure minimised soil settlement risks and reduced the environmental impact of heavy machinery use. -
Acoustic Challenges
Lightweight CLT required innovative acoustic treatments, such as the Batten & Cradle™ flooring system, to meet Building Code requirements.Structural Optimisation
Collaboration among engineers, architects, and contractors led to effective integration of structural and acoustic solutions. -
Fire Safety
Early engagement with fire engineers streamlined compliance, though site-specific detailing required additional effort.Moisture Management
The use of weather-tight external systems ensured durability and protection from elements. -
Team Engagement
Early contractor involvement was critical for planning, prefabrication, and coordination between trades.Detailed Planning
Service penetrations and other design details required significant upfront effort but ensured smoother on-site execution. -
Expanding CLT Use
The project demonstrated the viability of CLT for a variety of designs, encouraging its consideration in future builds.Market Evolution
The availability of improved “off-the-shelf” solutions since the project began underscores the growing maturity of the CLT market. -
Demonstrating feasibility
This project serves as a reference for the cost, environmental, and practical benefits of mass-timber construction, encouraging broader industry adoption.Standardisation and supply chain
Increased market competition and improved prefabrication methods are making mass timber more accessible and competitive. -
Positive Experience
Despite challenges, the developers and contractors expressed confidence in using CLT again, citing its sustainability, speed, and ease of construction.Lessons Learned
Acoustic design should start earlier, and standard solutions should be sought for smoother implementation and compliance.
Kevin Hickman Retirement Village
-
Time Savings
Mass timber construction saved 50% of the time required for the superstructure erection compared to traditional concrete methods. Contractors also reported faster installation of services, due to comparative ease of drilling and fixing into timber rather than reinforced concrete.Cost Considerations
Mass timber introduced a cost premium due to additional fixings, corbels, and fire-rated linings. However, early contractor and supplier involvement (ECI/ESI) was identified as a key method for mitigating these costs in future projects.Reduced Transport and Site Work
Truck movements were reduced by 65%, and on-site hours for the timber structure construction decreased by 45-55%. -
Carbon Reduction
The mass timber structure achieved a significant carbon saving, with 666,589 kg CO₂e compared to 2,039,150 kg CO₂e for concrete and steel.Lower Material Weight
Timber reduced the structural weight by over 50% compared to concrete, enabling lighter foundations and reducing environmental impact. -
Acoustic Performance
SoundDown™ acoustic systems ensured compliance with NZBC standards (STC 55, FSTC 50) for intertenancy walls and floors, demonstrating timber’s capability to meet sound insulation requirements. -
Fire Safety
Initial designs required full encapsulation with fire-rated plasterboard, but the revised approach minimised encapsulation to essential areas (e.g., corbels and beams) while meeting compliance.Moisture Control
A consistent approach to moisture management and early planning were critical, especially for areas exposed during construction. -
Design Coordination
Early involvement of contractors and suppliers was crucial for optimising design, addressing challenges, and expediting decisions.Service Integration
Service route coordination for timber structures proved more complex than anticipated, emphasising the need for upfront planning. -
Prefabrication
CLT and LVL prefabrication improved on-site efficiency, with pre-assembled panels allowing immediate usability and reducing waste.Material Innovation
Use of advanced acoustic and fire-resistant systems highlighted timber’s adaptability to meet stringent residential requirements.Seismic Design
Tectonus seismic connectors and vertical seismic joints provide designed seismic damping for the structure. -
Scaling Challenges
Limited suppliers in New Zealand highlighted the need for more competition and flexibility in sourcing materials. Supply chain challenges emphasised the importance of early supplier engagement.Knowledge Sharing
The project underscores the value of educating industry professionals on timber’s benefits and addressing misconceptions about its performance and estimated costs. -
Improved Work Environment
Workers found timber structures cleaner, quieter, and more pleasant to work with compared to concrete.Enhanced Living Spaces
The lighter, more sustainable materials contributed to a warmer, more aesthetically pleasing residential environment.
THE LIVING PĀ
-
Prefabrication Benefits
Mass timber elements such as CLT and LVL were prefabricated, enabling quick on-site assembly. Floors were trafficable immediately after installation, unlike concrete slabs requiring curing time.Coordination Challenges
The project highlighted the need for early and precise design coordination to prevent costly and time-consuming changes during construction. -
Carbon Footprint Reduction
Engineered timber significantly reduced embodied carbon. The project aligns with the Living Building Challenge (LBC) by using low-carbon materials and prioritising operational carbon neutrality through features like on-site solar power and closed-loop water systems.Regenerative Design
The building contributes positively to the local ecosystem by integrating ethnobotanical planting and displaying real-time energy performance data to promote sustainability awareness. -
Acoustic Solutions
Timber’s natural properties required additional treatments like raised floors and acoustic panelling to manage sound transmission in a complex, multi-use space. -
Fire Resistance
Timber members were designed to char predictably during fires, ensuring structural stability. Critical fixings were recessed to protect them from high temperatures.Moisture Monitoring
Consistent monitoring of moisture levels during construction was crucial. The team employed wireless sensors and moisture probes, refining their approach throughout construction. -
Integrated Design Process
The project’s complexity necessitated early involvement from contractors, consultants, and suppliers, fostering innovation and addressing challenges in real time.Cultural Partnership
Collaboration with Te Herenga Waka Marae ensured the integration of Māori values such as kaitiakitanga (guardianship) and Papatūānuku (Earth Mother) into the design and construction phases. -
Expanding CLT Use
The project demonstrated the viability of CLT for a variety of designs, encouraging its consideration in future builds.Market Evolution
The availability of improved “off-the-shelf” solutions since the project began underscores the growing maturity of the CLT market.Seismic Resilience
Innovative structural solutions, such as timber combined with ductile steel elements, addressed seismic challenges, particularly in Wellington’s earthquake-prone environment. -
Raising the Bar
By pursuing LBC certification, the Living Pā sets a precedent for ambitious, holistic sustainability goals, driving innovation in construction and design.Advocating for Change
The project emphasised systemic thinking, urging industry stakeholders to move beyond incremental improvements and embrace transformative practices. -
Design and Certification Synergy
The project revealed that achieving LBC certification requires a fundamental shift in traditional construction approaches, demanding rigorous collaboration and advocacy.Knowledge Sharing
Challenges such as moisture management and coordination complexities underscored the need for industry-wide learning and standardisation.
kowhai falls
-
Cost Comparison
The mass timber structure (LVL and Glulam) was comparable in cost to steel and concrete alternatives. Although requiring more initial work, it reduced overall construction complexity.Time Savings
Prefabrication helped streamline the construction process, but adjustments for weather-sensitive materials like LVL added to the learning curve.Economies of Scale
The project team plans to use the same timber structure for subsequent stages, indicating confidence in its cost and time benefits. -
Carbon Reduction
The building achieved less than 30% of the carbon emissions of a concrete and steel equivalent, with an embodied carbon footprint of 262,553 kg CO₂e compared to 853,517 kg CO₂e for steel/concrete.Sustainability Features
The design incorporates solar panels, PIR insulated panels (R4.8), and an advanced HVAC system, ensuring low energy use over its 50-year design life.Live Feedback
A unique feature displays real-time solar energy production and power consumption for public awareness. -
Hybrid Approach
The building combines mass timber with other materials for optimal strength and durability, demonstrating its versatility in commercial applications.Structural Innovation
Prefabricated LVL and Glulam elements allowed for a lightweight yet robust structure suited to the project’s requirements. -
Moisture Sensitivity
LVL’s responsiveness to weather required new systems and processes, with the team adapting construction practices for long-term durability.Fire Resilience
Engineered timber’s inherent fire resistance through predictable charring rates was used to develop an appropriate and complying fire design to add to its safety profile. -
Team Learning Curve
This was a first-time experience using mass timber for a large-scale commercial project for Dobbyn Builders. The team adapted quickly, leading to a successful outcome.Future Confidence
Positive results from Stage 1 have encouraged the continuation of the same approach for Stage 2, showcasing a significant learning curve. -
Energy Efficiency Monitoring
The integration of live energy monitoring is a standout feature, enhancing the building’s role as an educational tool for sustainability.Digital Tools
Prefabrication processes, though requiring precise coordination, highlighted the role of digital planning in achieving accuracy and efficiency. -
Encouraging Adoption
This project serves as a practical example of mass timber’s viability in large-scale commercial construction, addressing initial apprehensions through proven success.Visual and Functional Appeal
The project manager praised the aesthetic and structural qualities of timber, noting its superiority over traditional materials. -
Enhanced Shopping Experience
The choice of timber and sustainable design principles align with a modern retail environment that values aesthetics, energy efficiency, and environmental consciousness.
AVAILABLE TIMBER CASE STUDIES