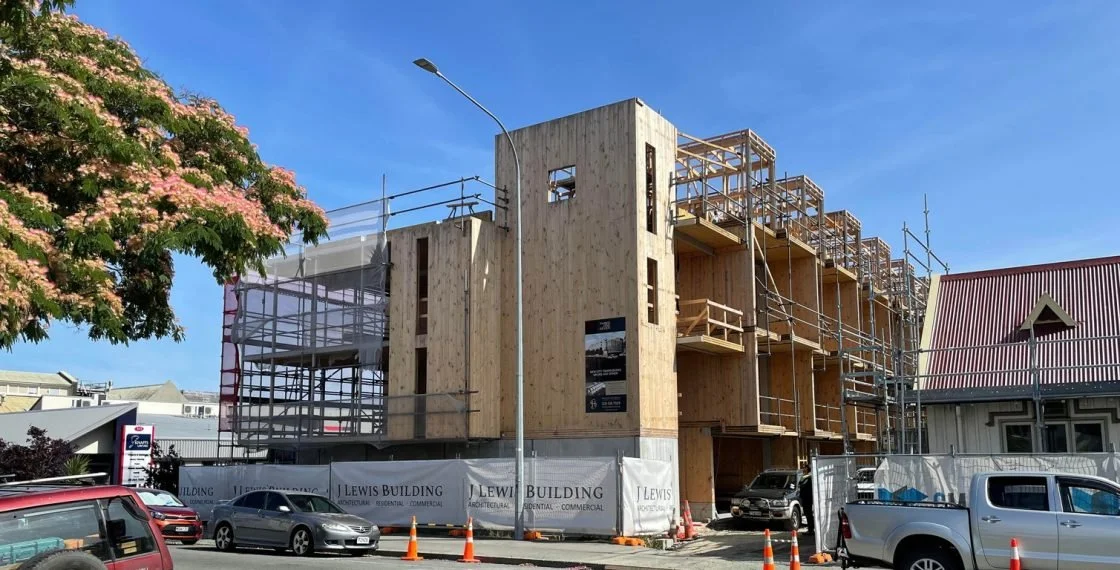
Hardy street development, nelson case study
IMAGE: Michael Smith
The Hardy Street development comprises eight 3-storey residential apartments, with one end apartment of individual design (Unit 1) and seven other virtually identical units (Units 2-8).
The basic structure is concrete foundations, ground floor slabs and low-level precast concrete walls, with extensive CLT walls and floors above, and stabilised in one direction by substantial steel frames. A range of timber framed internal fit-out and external walls which includes quite a complex range of materials and finishes.
What was the key driver for choosing to use CLT panels for this particular building and location?
The site ground conditions having a soft layer at a shallow depth required a lightweight super structure with a ground raft to mitigate long-term settlement issues that could arise from a heaver-reinforced concrete solution. The lighter weight CLT superstructure allowed increased speed of construction for lighter on-site cranage, shorter hook time and greater floor coverage per square meter per crane lift, with corresponding increased speed of construction when compared to a traditional reinforced concrete/metal deck construction. Zero temporary propping is required within the building footprint allowing for early access to the lower floors for storage of materials and fit-out.
Repetition of the superstructure and floor plate design allows for economies of scale to be achieved. Site Safety in getting the floor plates up quickly enabled working at heights to continue with a solid work platform in place and allowed work in lower areas to proceed safely at the same time.
How did the use of wood compare with the other material options?
The engineered CLT solution requires early contractor engagement to determine the most efficient construction methodology to take advantage of the lighter CLT panels of large surface area for quick erection and tight site access. General timberwork builders are able to understand the system and screw the building together without the need for erection specialists.
Prefabrication required more work up front including computer modelling, which was beneficial to share between specialised trades (Steel, Concrete panel, CLT). Once on site the co-ordination of all these trades went very well. Service penetrations were the one area in which we needed to provide more input and would change that in the future.
Speed in getting up and out of the ground, and safety of construction workers once up, limiting scaffold use to the external fabric. New material learning by all involved has meant the need for all parties to keep co-ordinating along the construction process. Detailing has continued as methods on site have evolved/ changed, which has sometimes been driven by Building Consent Authority site questions.
How did you find the consent process in regard to your specification of wood?
The client arranged for an Engineering Consultant experienced in timber design to carry out a Structural Peer Review of the structure to B1 of the Building code and a PS2 Design Review was submitted to the Building Consent Authority (BCA).
Fire Design early engagement allowed for early resolution of fire compliance detailing.
On-site understanding by the Building Consent Authority still needs work. Questions and comments on site have slowed construction as it isn’t the norm, especially around the detailing of weather-tightness and this product. Building Consent Authority often defaults back to lightweight timber construction when unsure. This has added time on site in resolving or added costs to comply or provide the detailed reasoning of design decisions.
Acoustic design compliance needed to be considered earlier, so there was time to investigate more options. This highlighted the need for more “standard” lightweight methods to achieve compliance, rather than mass, again consultants learning as we went but better options are available now on the market.
4.0 Would you consider wood to replace other material options in future buildings; and if so, why?
Engineered Wood over the last 15 years in New Zealand has become an established construction material and can be incorporated into multiple design solutions for the superstructure of many building structural forms when the engineered wood is installed and protected appropriately from the elements. Engineered wood’s strength-to-weight ratio combined with its ease of workability, speed of erection and ability to sequester carbon make the incorporation of engineered wood products into projects “a must consider rather than a nice to have”.
The available ‘off the shelf’ solutions are specific for CLT since designing has improved considerably since this project was commenced (especially acoustic options), which has made the system more usable and easier to detail, and get through the consenting process.
The use of other engineered timber materials has increased with suppliers providing materials and systems that can be easily designed and used.
Overall based on the project experience, and for similar construction would we use it again, yes. Would we do it the same way? Probably not, as there was some detailing that wasn’t suited to the products used and more effective solutions are now available.
key learnings & insights
-
Cost Comparison
While CLT had higher upfront material costs, the overall cost was competitive due to faster construction times and lower Preliminary & General (P&G) expenses.Time Savings
CLT construction allowed faster erection due to lightweight panels and prefabrication, reducing time on site and improving project efficiency.Economic Scaling
Repetition of the superstructure design across seven similar units enabled economies of scale. -
Carbon Sequestration
The project sequestered 470 tons of CO₂, significantly reducing its carbon footprint compared to traditional concrete and steel alternatives.Waste Reduction
Prefabrication minimised material waste on-site, enhancing sustainability.Lightweight Materials
The lighter structure minimised soil settlement risks and reduced the environmental impact of heavy machinery use. -
Acoustic Challenges
Lightweight CLT required innovative acoustic treatments, such as the Batten & Cradle™ flooring system, to meet Building Code requirements.Structural Optimisation
Collaboration among engineers, architects, and contractors led to effective integration of structural and acoustic solutions. -
Fire Safety
Early engagement with fire engineers streamlined compliance, though site-specific detailing required additional effort.Moisture Management
The use of weather-tight external systems ensured durability and protection from elements. -
Team Engagement
Early contractor involvement was critical for planning, prefabrication, and coordination between trades.Detailed Planning
Service penetrations and other design details required significant upfront effort but ensured smoother on-site execution. -
Expanding CLT Use
The project demonstrated the viability of CLT for a variety of designs, encouraging its consideration in future builds.Market Evolution
The availability of improved “off-the-shelf” solutions since the project began underscores the growing maturity of the CLT market. -
Demonstrating feasibility
This project serves as a reference for the cost, environmental, and practical benefits of mass-timber construction, encouraging broader industry adoption.Standardisation and supply chain
Increased market competition and improved prefabrication methods are making mass timber more accessible and competitive. -
Positive Experience
Despite challenges, the developers and contractors expressed confidence in using CLT again, citing its sustainability, speed, and ease of construction.Lessons Learned
Acoustic design should start earlier, and standard solutions should be sought for smoother implementation and compliance.